After 15 years of active service, the Danish Navy needed to re-fit and modernize technology aboard the Absalon-class support ship. Logimatic and ThinManager make it happen.
Category: Customer Story
This is a collection of real world stories from facilities that have used ThinManager.
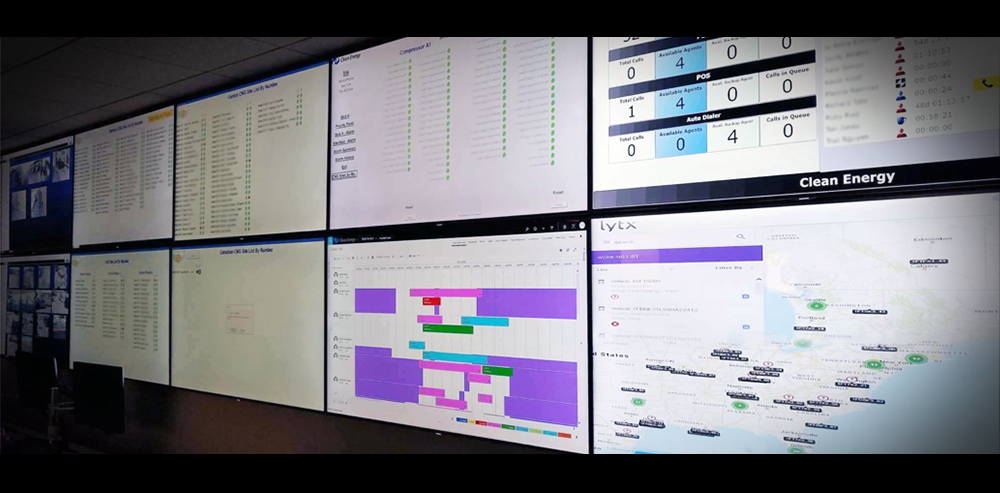
System Integrator Uses ThinManager and Thin Clients to Increase Visualization, Cut Costs for National Operations Center
The Setup
When Robert Maxfield first learned about his customer’s desire to create a modern national data operations center, the customer already had some idea of how they would want it to be built out. The original idea included a ton of expensive video hardware that would be able to drive video output cards capable of running several high-definition TVs.
This solution had several shortcomings. The first issue was that it was going to be very expensive. Secondly, the timeline to procure the hardware and configure it was very lengthy. Finally, even after all the expense, the system would not be very flexible if new applications needed to be added in the future. Enter, Robert Maxfield from WachsField Technologies.
Maxfield, a seasoned system integrator, had used ThinManager on previous projects with great success. He knew the end result his customer was seeking could be achieved at a lower cost. He also knew that if they ever wanted to easily scale up from the initial design, they would need a better plan than just continuing to purchase overpriced video display and routing components. After discussing the new plan with the customer, WachsField Technologies developed an alternative design leveraging ThinManager and Arista thin client hardware.
WachsField was tasked with creating an operations center with ten 60’ high-definition TVs that would be used as monitors. The customer had thirteen different applications that would need monitoring including GE IFIX HMI, Proficy Web Trending, Call Center Applications, GSA system, work order programs, mapping software, IP cameras and more.
The Deployment
Using ThinManager, WachsField Technologies was able to configure secure connections to the company’s datacenter to provide displays to all ten 60” monitors. “Using ThinManager’s MultiSession, MultiMonitor and Tiling features, we were able to divide the screens in various configurations according to the client’s needs,” stated Maxfield. “Each station at the NOC was outfitted with a laptop and an iPad. The iPads are running ThinManager iTMC and are able to Shadow the larger screens—bringing pertinent data right to the station. This also allows for the NOC staff to modify the layouts on the larger overall screens.”
WachsField also deployed two additional ThinManager features to enhance security and improve the end user experience. The first was WinTMC. Just like iTMC can be installed on iPads, WinTMC can be installed on PC workstations and laptops. This allows ThinManager to centrally manage and deploy applications to those devices in the same way they are deployed to thin clients. In this case, the end users can easily switch between applications local to their laptop workstations and those being delivered by ThinManager.
The second was AppLink. This is a simple ThinManager setting that removes access to the desktop when deploying applications to thin clients. By using this option on the thin clients that drive the large operations center displays, only the required applications are displayed. This reduces the potential for end user error and keeps the NOC staff focused on their jobs.
“The operations center is now running day in and day out utilizing ThinManager. ThinManager’s technology saved the client thousands of dollars and allows for extreme flexibility such as adding new IP cameras feeds as new cameras are installed and new stations come online,” Maxfield explained. “We will continue to use ThinManager whenever we can. Our customer decided it was the best solution for their national operations center based on flexibility, scalability, cost and simplicity. This project was a success on all those points.”
Project Overview
ThinManager deployment to expand visualization for new National Operations Center:
- ThinManager Redundant servers
- 4 – Arista BoxPC 240 thin clients, unlimited client connections
- 10 – 60” high-definition TV monitors
Fit for ThinManager:
System Integrator Uses ThinManager to Help Create a New Platform for Benchtop and Small-Scale Bioreactor Users
Because of these things and much more, successful SIs learn how to work very efficiently. When a tool or system can be utilized to make projects more streamlined, SIs will seek to redeploy that tool or system on other projects to help overcome the obstacles mentioned above.
In the course of providing solutions to customers, Panacea Technologies not only found a great technology to improve their customer’s computing, they also found a way to create a new offering that has the potential to change the benchtop and small-scale reactor space for the better. That technology is ThinManager from Rockwell Automation.
The Challenge
The current state of the benchtop and small-scale bioreactor market allows limited interaction with the reactors. Some facilities may have hundreds of reactors that need to be controlled and monitored. The issue is that these systems often use proprietary HMIs that have rigid limitations on how many units can be connected. Currently, many operators simply have to deal with monitoring one or two bioreactors at a time from a fixed terminal.
“We once saw an operator running around with kitchen timers, paper notebooks, and a Microsoft Surface all while standing in front of the proprietary HMI,” said Will Aja of Panacea Technologies.
Besides making lab operations inefficient, these systems have no real way of controlling user access. Panacea Technologies decided they could apply ThinManager to help solve these issues. What they have developed is not only a solution, but a whole new product to offer to their pharmaceutical customers.
The Solution
Panacea knew that mobile tablets would be an excellent way to overcome many of these issues. But seeking more than just a mobile connection, Panacea also wanted to provide access to more reactors at a time.
“We envisioned a product where scientists could move freely through the lab interacting with all the Bioreactors in a lab quickly with an intelligent system that would know who had access to what based on where they were. ThinManager fit the bill perfectly here, and we are taking advantage of almost every single feature ThinManager offers.”
Chevron North America Exploration & Production using ThinManager to power production
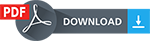
Since 1879, Chevron has been on the cutting edge of exploration and innovation. Over the years they have grown and changed with the times and have always continued to evolve along with the needs of the world. Today, they are not only one of the largest companies in the world; they are a global leader in technology. When Chevron needed a new technology for plant management, they chose ThinManager.
Time to Upgrade
For years, Chevron had used custom built remote units for their facilities to work within custom parameters specific to their industry regulations. After years of dealing with the added resource cost in cash and labor, a project manager made the suggestion to switch to thin clients as a hardware solution at a specific plant. The suggestion was met with approval and they began the task of searching for a thin client management platform that could meet their needs.
Another Great Discovery
After using the same HMI over the last decade for their basic platform and integration services, it was time to look beyond the known and find the next piece of the puzzle. While searching and calling around to other software companies and integrators, they encountered the answer in their own backyard. The ThinManager Roadshow came to town, and after experiencing the hands-on demonstration and seeing ThinManager in action, the decision was made to begin implementation. The decision to change from PC “fat clients” to a complete thin client install was made for them by the sheer effectiveness of the ThinManager platform demonstration they attended.
Measure Twice, Cut Once
Deciding to not rush into anything, Chevron decided to move forward with a single plant deployment of ThinManager. “My intent with this project was to get the most out of every piece of technology,” said B.K. Wallace, the Infrastructure Server Analyst overseeing the project. He brought in new servers and updated to InTouch 10 and Windows server 2008. Then, with the help of his current HMI integrator, he began tying together all his systems to take advantage of the ThinManager MultiMonitor feature. After initial testing, everything worked well together and full test deployment was underway.
Planning for Success
The goal for the planned integration was to install two Terminal Servers and thin clients in place of eight PC “fat clients” and to deploy ThinManager in conjunction with their HMI software. By making use of MultiMonitor, IP Cameras, and TermSecure, they planned to set up an efficient and secure operation by using Smart HID cards to create an audit trail while allowing for a supervisor to view what was happening at every station via a centralized terminal that could display 5 client screens simultaneously. “Before, we could only shadow a single HMI with our old brick,” stated B.K. Wallace.
More than Affordable
Even while looking to build the most modern system available, cost was still a factor. Over the course of deployment, they were able to sell their old licenses to defray upgrade costs. By purchasing a Mirrored 5-Pack of ThinManager 5.0 XLi licenses from ACP, they were able to take advantage of every available ThinManager feature. With the additional purchase of COMP Support for 1 year, they not only receive one year of support, but also get all version upgrades at no cost. “The first thing I plan to do when we complete deployment is to upgrade our other plants with ThinManager 6.0.”
What about Tomorrow?
Even though they are still completing their test deployment by running the platform in parallel to their current system, they are already looking into the future. With a process control group that spans from Alabama to Wyoming, and 180 servers, there is room for a massive deployment in the future. “This plant will be the footprint for all our CO2 plants around the country.”
ThinManager Technology Simplifies Operations at City of Riverside
The wastewater treatment plant for the City of Riverside, California processes approximately 33 million gallons a day at a facility with preliminary, primary, second- ary and tertiary treatment. Solids handling for the facility includes anaerobic digestion and mechanical dewatering.
The 1,000 foot elevation change across the plant’s service area makes com- munication with the system’s 22 lift sta- tions a challenge. The plant also manages a 3.3 MW co-generation facility and the City’s closed landfill operation. The work is detailed, complex, and the continued smooth operation of the facility is impor- tant to both the community and the local environment.
“We have the same issues as any other wastewater treatment plant,” says Steve Schultz, the City’s Wastewater Systems Manager. “We have a limited reserve of funding and we try to tackle the facility expansion with internal staff whenever possible.”
The Challenge: Simplify SCADA Maintenance and Updates
In 2002 the plant’s SCADA operations were disjointed – coordination and mainte- nance were difficult and expensive. Changes to one system were often not replicated on other systems. As a conse- quence, SCADA operations could best be described as disparate, unconnected and often unreliable. Loss of data was not uncommon, which presented a significant problem for a facility with several critical reporting requirements.
Emory Scriven, Project Manager for WaterHammer, Inc., consulted with The City of Riverside and described the prob- lem this way: “We had around 15 stand- alone PCs throughout the plant. With all of the problems of continual updates, new service packs, and new drivers, there were naturally high maintenance costs”.
Steve Shultz agreed. “Just the ability to move information from one treatment
process to another area within the facility was problematic. We wanted a centralized server and a more economical way to view the system from within the plant. Where I worked before in San Bernardino, CA, they have the Thin Client system and it seemed to be what we needed here.” And once again, ACP’s ThinManager met the require- ments exactly.
The Solution
ACP’s Thin Client management and enabling software, ThinManager, allowed the City of Riverside to focus on the process, not fight with computers. ThinManager also helps the City manage their Terminal Servers from within the same user interface that they use to man- age all of the Thin Clients.
By replacing failure prone PCs with ThinManager Ready Thin Clients the staff was able to greatly simplify their daily oper- ations and reduce costs. Thin Clients, with no moving parts and no local storage, improved reliability and reduced down- time. Adding new interfaces is as easy as plugging in a Thin Client and turning it on, giving immediate access to the existing software and data. This ease of expansion gives them a way to plan for the future with a redundant system.
Future Plans
Schultz and his team are considering adding the Laboratory Information Management System to the SCADA sys- tem. The move to Thin Client technology shortens the development cycle, lowers costs and gives improved reliability. With ThinManager, redundancy is built-in, and the City can do development work from any terminal. The Thin Clients give the flexibility to install nodes wherever there’s fiber optic cable available. With Thin Clients and ThinManager, the City of Riverside can finally focus on the controls and instrumentation side of the SCADA sys- tem and keep the entire processing plant running smoothly.
ACP ThinManager helps Shurtape plan for the future
Evolving out of a business started in 1880 near Hickory, North Carolina, Shurtape Technologies, Inc. today manu- factures a wide range of quality paper masking, polypropylene, coated vinyl, metalized cloth and duct tapes. These products service a variety of adhesive tape applications in many markets, including automotive, HVAC and construction, power and utility and military and aero- space industries.
Why a change was necessary
To meet the growing needs of their customers, Shurtape invests aggressively in new technology and equipment. Using automation, simplicity and effi- ciency as guiding principles, Shurtape reviews their process with the goal of producing the finest tapes in the indus- try, while satisfying customer require- ments for highly competitive pricing, dependable quality, reliable performance and rapid delivery.
Constant expansion and improve- ment bring continuing change and sys- tem enhancements. Delivering new machine interface screens and display stations on a regular basis is difficult at any time, but in an active manufacturing facility this must be done with as little disruption in production as possible. There are also unusual physical con- straints faced when new displays and computers are required around an exist- ing production line.
Finding a way to rapidly bring new dis- plays online under these conditions meant that Shurtape had to find a system that would install in limited space and in less time than a traditional PC. And the solu- tion had to be both cost effective and reli- able. ACP’s Thin Client solution meets all of these requirements.
Implementing ACP Technology
The move to Thin Clients started in April 2001 and has continued to evolve. The clients are located throughout the facility and use Wonderware to display information from as many as eight different PLC’s. Because of the centralized software model inherent in the Thin Client architec- ture, new display stations go online in record time. Each time a new interface point is identified it is only a matter of installing another Thin Client, touch screen, and cable. No new software has to be installed.
Five Windows 2000 Servers host all of the Advantech industrial Thin Clients used at the plant. The small size of the Advantech clients coupled with their resistance to vibration and heat makes them easy to mount almost anywhere – a must when working in cramped condi- tions.
Thin Client Benefits
Before switching to Thin Clients it took approximately three hours to load and configure the appropriate PC software each time a new display was required. With Thin Clients a new display can be added by simply plugging in a new Thin Client and turning it on. A new Terminal Server can even be configured in less than four hours. Also in the unlikely event of a Thin Client failure, downtime is drastically reduced compared with the time required to correct a PC failure.
Switching to Thin Clients resulted in project cost reductions of 40%, and Shurtape now has the ability to display information across the plant with a very low cost effective solution—one that is also very easy to configure.
One of Shurtape’s business principles is to invest in the most cost effective manu- facturing technology that will produce value-engineered products. ACP is proud to be able to help them meet this goal by providing a Thin Client solution that will save them money year after year.
ACP Thin Clients Bring Cost Savings to PCS Nitrogen
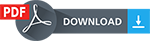
Using a single raw material, natural gas, the Georgia based ammonia plant for PotashCorp, PCS Nitrogen, is the largest producer of nitrogen products on the East Coast. Since its start-up in the late 1970’s this plant has become one of the most reli- able ammonia plants in the world, and now produces over 2.8 million tons of ammonia and ammonia based products each year.
The Challenge: Reduce Maintenance and Expansion Costs and Increase Functionality with Zero Downtime
“Ammonia is a commodity chemical and typically the margins are not great,” offers Keith Wilson, Ammonia Technology Manager at PCS Nitrogen, “so the keys to making money are having a very efficient plant and having a very high stream factor. And this plant has had a stream factor in the 98 to 99 percent range for the last three to four years.”
By the end of the ‘90s, however, the plant required a major upgrade in its con- trol systems – the 1970’s vintage computer system was demanding a great deal of money in maintenance dollars just to keep it running. For the plant to protect its incredible on line record, the control and monitoring systems had to be replaced and improved.
Implementing ACP Technology
Replacing the aging, unreliable com- puter system (which provided the operator interface) with state-of-the-art DCS tech- nology decreased current 5 minute scan times to under 10 seconds. Moving to Thin Client technology at the same time allowed PCS to easily and inexpensively distribute the new displays throughout the plant while still being able to use their lega- cy Windows software. Adding additional monitor screens simply means plugging in a new Thin Client – no software has to be installed or even modified.
One of the central elements of the plant’s original control room was its panoramic display – the several walls of gauges and alarm panels that make up this feature have long been a staple of chemical processing plants. PCS realized that there were substantial economic and perform- ance benefits to be realized if some of the existing instrumentation could be replaced with Thin Client hardware, so they began using Thin Client technology to give the operator the look and feel of single loop controllers and strip chart recorders at approximately one-third the cost.
“With ACP Thin Client technology,” offers Anderson, “we can deploy lots of small, single entity monitors that give our operators the panoramic view they want at a much reduced cost.” Combined with the additional monitors, Thin Client technology serves the partic- ular needs of PCS Augusta perfectly. In most cases, the user cannot tell the dif- ference between a Thin Client applica- tion and an application resident their own machine. All this without a single day of lost time production.
Future Plans
“Our intention at this point in time is to continue to use the Thin Client tech- nology when we implement the DCS sys- tems throughout the plant,” says Anderson. Using Thin Client technology to provide multiple monitors gives the operators a better insight into their process. PCS also plans to use the Thin Client technology to give operators a view of the entire process from any location, using field mounted, hardened monitors on all their local control panels through- out the campus.
At PCS Augusta, plant operations move continuously, and so does all of their man- ufacturing data. The combination of the new DCS system and ACP Thin Client tech- nology gives PCS a competitive edge . . . and keeps their business operations smelling sweet.
Logan Aluminum Rolls Out ACP Thin Client Technology
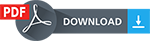
Named for the county in Kentucky where it made its home in the early 1980’s, Logan Aluminum, a joint venture between Arco Aluminum and Alcan, specializes in the production of rolled aluminum. The 1.5 billion pounds of metal that passes through this plant each year makes up about 1/3 of the rolled aluminum used by the entire US aluminum can market.
The Challenge: Update the Aging HMI System Without Affecting Production
The Logan Plant only shuts down only one day each year, and new products must be installed without risking Logan’s World- Class Production and Utilization numbers. Like many factories, Logan was using PCs throughout to monitor and control pro- duction, but the management team was becoming tired of system updates and ongoing PC maintenance. Whatever HMI they settled on, they wanted a way to dis- tribute the user interface without relying on the traditional distributed PC model.
Implementing ACP Technology
The Logan Automation Team had been reading up on Microsoft Terminal Server technology and realized that it would allow them to replace their PCs with Thin Client terminals. The benefits that a Terminal Server system could bring to their installa- tion were evident – any new interface soft- ware installed on a single server but dis- played on multiple Thin Clients was their solution to software maintenance.
During this process, Intellution was chosen as the HMI provider, and the Automation Team set up a server with Windows NT 4.0 TSE to test for compatibil- ity with the Intellution products, as well as with their existing HMI software. To save money during this pilot project, Logan used existing Windows computers as Thin Clients. This allowed them to rapidly con- figure a test bed for all of their evaluations, and it soon became apparent that a Thin Client system would be a stable and capa- ble platform for the project.
After seeing demonstrations of Intellution software running on ACP Enabled Thin Clients, Logan had the assur- ance that the pieces of this project would come together as they had hoped. ACP Enabled Thin Client hardware and ACP’s ThinManager management software would be the perfect compliment for the proposed HMI Terminal Server setup.
Implementation of the new Thin Client based HMI system began, and when they were finished with the first phase of the installation, the Hot Mill section of the plant had 3 Compaq 6400R servers for the user interface screens and 2 Compaq DL 380 for the Intellution SCADA servers. Each 6400 was outfitted with dual 500 PIII Xeon processors with 1 GB of memory, while the DL380’s have dual 733 PIII processors with 512 MB of memory. All communications between the Thin Clients and the servers is across a 100MB-fiber net- work.
One of the user interface servers runs a user interface written in Microsoft’s Visual Basic, another runs Intellution’s standard iFIX product. The third server uses the Server Failover functionality built into ACP’s ThinManager to serve as backup for the other servers.
Future Plans
Logan’s Hot Mill Automation Team worked closely with ACP to collect the information that they needed to get all of the software up and running to their satis- faction. ACP provided key contacts at Intellution, was a major player helping Intellution with the development of their TSE product, and remains active in Logan’s expansion project.
Because of the success of this initial Thin Client project, other business units at Logan Aluminum are now considering a Thin Client Solution for their operator interface upgrades. Once these units are converted, Logan Aluminum will have fifty or more ACP Enabled Thin Clients installed and running under ACP’s ThinManager.
Forklifts give new meaning to “Mobile Computing”
Imperial Tobacco Canada has been Canada’s leading tobacco company for over eighty years, producing two-thirds of Canada’s cigarettes including du Maurier, Players, and Matinee.
Imperial is currently running a cigarette manufacturing plant in Guelph, Ontario, and a tobacco processing facility in Aylmer, Ontario. Their corporate office is in Montreal.
The Challenge: Deploying Inventory Management Software on Moving Forklifts
Imperial Tobacco was dispatching fork- lifts to move materials and products with an old-fashioned paper-based requisition and confirmation system. A computer- based system would be faster and more responsive, with greater accuracy and easi- er record keeping.
The problem – mounting a computer on a moving forklift. PCs are large, and the vibration and movement of the forklifts are extremely damaging to hard drives. ThinManager Ready Thin Clients provided the solution.
Implementing ACP Technology
Imperial researched Thin Clients and found that ACP provided the features that they needed. They attended an ACP Forum to learn the details and then set about deploying Thin Clients on the forklift project.
They chose Xycom XA3412T units with an integrated touch screen, powered with 24v DC from the forklift. The units con- nect to the network through an Enterasys RoamAbout wireless transmitter. This com- municates with the wireless network that Imperial already had in place.
Additionally, each unit has a long range barcode scanner attached to its PS/2 port. This allows the driver to scan material from the forklift and have it qualified by the material verification program running on the terminal server.
The Xycom Thin Client displays a brows- er that shows a Java Flash application (run- ning on a server in Montreal) that allows the driver to receive instructions from the Inventory Management system while driv- ing. He then uses the tethered scanner to verify that the right material is picked up, and then delivers it to the needed location. This mobile forklift deployment has been installed on sixteen forklifts as of this writing.
Reliability is a key issue, so a second tier of scanners was installed on stationary Thin Clients. These wireless scanners connect to a base station that is attached to the PS/2 port of a Xycom XA1300 ThinManager Ready Thin Client. If the forklifts are unavailable, an operator can carry the wire- less scanner to verify the material. The data are sent to the base station and into the system through the Thin Client.
Future Plans
Since the initial deployment, Imperial Tobacco has expanded their usage of ACP several times in Guelph, including deploy- ing ThinManager Ready Thin Clients as HMI workstation upgrades.
One feature that Imperial likes is the Thin Client’s flexibility. Units can be given unlimited access, applications, and resources, or can be limited to a single application with simple settings.
Additionally, the remote management and administration has simplified manage- ment and maintenance. Because patches and upgrades are performed on the termi- nal servers, not the clients, less time is wast- ed walking to the nodes for management.
Imperial also expanded to a second site, the tobacco processing plant in Aylmer. Because the two sites share a Wide Area Network, Thin Clients and Terminal Servers at the Aylmer site can be moni- tored, managed, and even shadowed from the Guelph site.