The Desire for Virtualization Drives ThinManager Centralized Management in Ireland
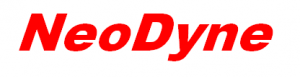
For decades, industrial automation in North America has seen consistent growth in both volume as well as technological development. In many parts of the world, however, there has been a slower adoption rate of these new innovations in the manufacturing sector. One such innovation, Virtualization, has forced companies to reexamine their stance on waiting to adopt new technologies.
Enter NeoDyne, located in Cork, Ireland. Specializing in creating production performance monitoring and process improvement solutions, this fifteen year old system integration firm has plunged into these new technologies head first as they continue to modernize facilities across Ireland. One of their current deployments is a Manufacturing Information System (MIS) at the main processing facility owned and operated by a global leader in the cheese and whey protein market.
Martin Farrell, the Automation Director at NeoDyne, explained to us how their customer’s desire to virtualize brought them to adopting the ThinManager Platform. “The IT managers at their main facility had been trying to support all their standalone SCADA systems for the last 20 years. Very early on in the planning process they decided they wanted a virtualized environment without physical servers sitting on the plant floor. They were looking to bring all of their applications into a VMware virtualized environment that would deliver their applications to the plant floor. At that point we advised them to adopt thin clients to replace their standalone PCs.”
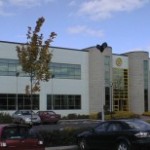
It became obvious to the team at NeoDyne that updating the network infrastructure while implementing a Wonderware System Platform based architecture in a virtualized environment was going to require a centralized management solution. “We had limited experience with Terminal Services and thin clients before this deployment but knew that this was the direction we had to go. We did research, read a lot of articles and found ThinManager. It has turned out to be a fantastic product that allowed us to tie everything together. It is an intuitive software platform that makes configuration and management easy,” said Martin.
Once deciding to implement all of these platforms, the first step was to tackle the challenge of integrating them with their planned thin client deployment. Because the facility had three separate areas for cheese production, ingredients, and utilities, they decided to construct a network architecture using dual redundant I/O servers in each area from Solutions PT. “The facility is still very much a Unit based production outfit. Even though it is an automated plant, they still have a model of individual units and each unit requires its own dedicated control room. At the control level, it was a mix and match of everything, but we did put together a very organized structure on what had previously been a disparaged group of PLC platforms from Siemens to Allen-Bradley to Mitsubishi to ABB. ”
Once the architecture was firmly in place, Martin and the team at NeoDyne started applying a multitude of ThinManager Platform features to simplify everything and make the system more efficient. “We have 2 ThinManager Servers set up in a mirrored configuration so if a thin client for any reason fails to connect to one, it automatically connects to the other. If we go home at the end of the day and one of the servers fails, we know they won’t be in the dark and we have time to get it back online with minimum disruption to the operations.”
Martin then explained some of the other ThinManager Platform features they decided to take advantage of. “We deployed AppLink to deliver client sessions so the operators only have access to the InTouch Application without having to click around a Terminal Services session via the desktop to get to their SCADA application. We also use it to launch a particular application so if the session crashes it will automatically reboot the application.”
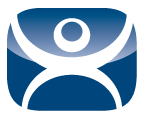
NeoDyne, like many others, also uses the ThinManager Shadowing feature to provide off-site assistance by being able to remotely log into an operator’s user session and guide them through problems in real time without having to be in the facility. However, they are also using it to reduce licensing overhead costs for their customer as well. “Something else we have done in the facility is to allow an operator to go between two control rooms without using additional licenses via the Terminal to Terminal Shadowing feature. We can have one session that is shadowed between two control rooms and depending on which Control Room he is in, he can take ownership of either application. These “part time” thin clients that are used infrequently can identify as a shadowed thin client to avoid purchasing additional licenses to maximize cost efficiency.”
Their next goal was to find a way to allow the facility managers and supervisors to view the application without needing to travel through the facility. ThinManager WinTMC made that a simple task without having to complicate the proposed facility network architecture. “The main benefit of deploying the WinTMC feature is that it allows the plant managers and supervisors to access the application session on their desktop PCs to monitor plant performance and switch back and forth without needing additional hardware. Also, as the PCs on the floor die they can replace them with thin clients instead of PCs as part of a continuing maintenance budget. It gives them flexibility on how and when they buy more hardware.”
Now, more than a year since they began this project, we asked Ciaran Murphy, Automation Systems Lead for NeoDyne, how further deployment of ThinManager has been unfolding at the facility. “What we have found is that using ThinManager to manage the thin client setup and the actual thin clients themselves down on the plant floor is allowing us to gradually retire more and more of their SCADA clients. Their existing control systems and standalone SCADA systems are actually still there. We put in a Manufacturing Information System (MIS) over the top to analyze plant performance. Now, having seen the benefits of this technology, they will gradually replace their existing Thick clients on the Plant Floor with Thin Clients. Over the next few years they will continue to replace the rest of the standalone PCs on the floor and just be left with thin clients.”
Now that ThinManager is efficiently driving the facility systems, we wondered what is next for the team at NeoDyne. Ciaran was more than happy to tell us. “With the success of this project, we showed other clients what ThinManager could do and are already deploying it into another ongoing project we are involved in with another major dairy here in Ireland who was impressed by the product. Going forward, all of our future platform solutions for the next 5, 10, 20 years will have ACP ThinManager Platform as a fundamental part of our standard system designs and we will actively propose it. To us there isn’t even a choice; if the site allows it, we will use ThinManager.”
ABOUT NEODYNE: NeoDyne Plant Information Management solutions enable end user Lean Manufacturing, Process Performance Improvement, Overall Equipment Effectiveness, and Cost Improvement business transformation initiatives. The NeoDyne solution is specifically tailored for milk / food processing and combines features to manage and provide traceability for food batch manufacturing in continuous/batch processes. Plant automation and Quality/LIMS and ERP systems are joined into one unified solution.
__________________________________________
To review cost savings of using the ThinManager Platform, visit our ROI Calculator here.
To read about successful ThinManager Platform deployments, visit here.
To see when the next ThinManager 2-Day Training Session is being offered, visit here.