The modern industrial enterprise is complex. Many contemporary manufacturers not only face the challenges that come with automation and ensuring that facilities remain secure, but they must also manage very strict validation procedures. While downtime can negatively affect any type of installation, a validated installation requires even more effort when new equipment is commissioned, or existing equipment must be updated or replaced.
Fortunately, companies like Huffman Engineering have built their business around providing innovative solutions for their customers’ validated environments. We recently spoke with Keith Mandachit, engineering manager at Huffman. Keith shared some insights into a recent project Huffman completed for a global pharmaceutical manufacturer.
“We specialize in regulated industries at Huffman,” Mandachit stated. “We have a utility division that serves facilities like water/wastewater and electrical utilities and an industrial division that focuses more on pharmaceutical/life sciences as well as food and beverage and material handling customers. This project focused on expanding and installing a fully qualified pharmaceutical line. Part of the integration of ThinManager was the inclusion of a fully qualified solution. The qualification included documentation from the start to finish (Validation Plan, URS, FS, IQ, OQ, and PQ).”
“One of the biggest pain points for the customer was managing Windows Updates with client computers out on the plant floor. Due to the sensitivity of the pharma quality and critical nature of keeping downtimes to a minimum, they did not allow the IT department to automatically push out Microsoft updates to their automation computers. A thin client solution allowed for expansion without increasing the workload of maintaining full-blown PCs with dedicated operating systems. The thin clients don’t have local operating systems, so the burden of validation and maintaining Windows updates is greatly reduced,” Mandachit continued.
“The integration was seamless. The most challenging part of the project was due to the end user’s implementation of cybersecurity segmentation and firewall rules within the system. The challenge was playing mediator between the IT and OT departments,” Mandachit added. “This is quickly becoming a role that sophisticated system integrator partners play in modern deployments. The convergence of IT and OT is a real thing. Being able to successfully communicate between these two parts of the organization is vital to success.”
Another challenge Huffman faced on this project was giving the automation group the ability to see what exactly is being run on the plant floor client computers. Better insight into plant floor operations would provide quicker and more efficient support and troubleshooting.
“We used a couple of ThinManager features to solve this issue,” Mandachit said. “By using ThinManager’s AppLink feature, we made sure that operators were only presented the applications they needed. Then we implemented terminal to terminal shadowing to allow the automation group to monitor or control any terminal remotely. They liked this feature so much, that we also set up an on-the-fly control room in one of the conference rooms without having to round up any additional equipment. ThinManager made the whole process very simple.”
“The thin client deployment using ThinManager to deliver FactoryTalk View SE was the best solution for this expansion. Not only did it simplify the validation issues, but it also provided the customer with more functionality than expected. Expanding their view and control over the process makes managing and troubleshooting much easier, and it added more value to the outcome for the customer.” Mandachit concluded. “ThinManager is the type of solution we can confidently recommend for our customers.”
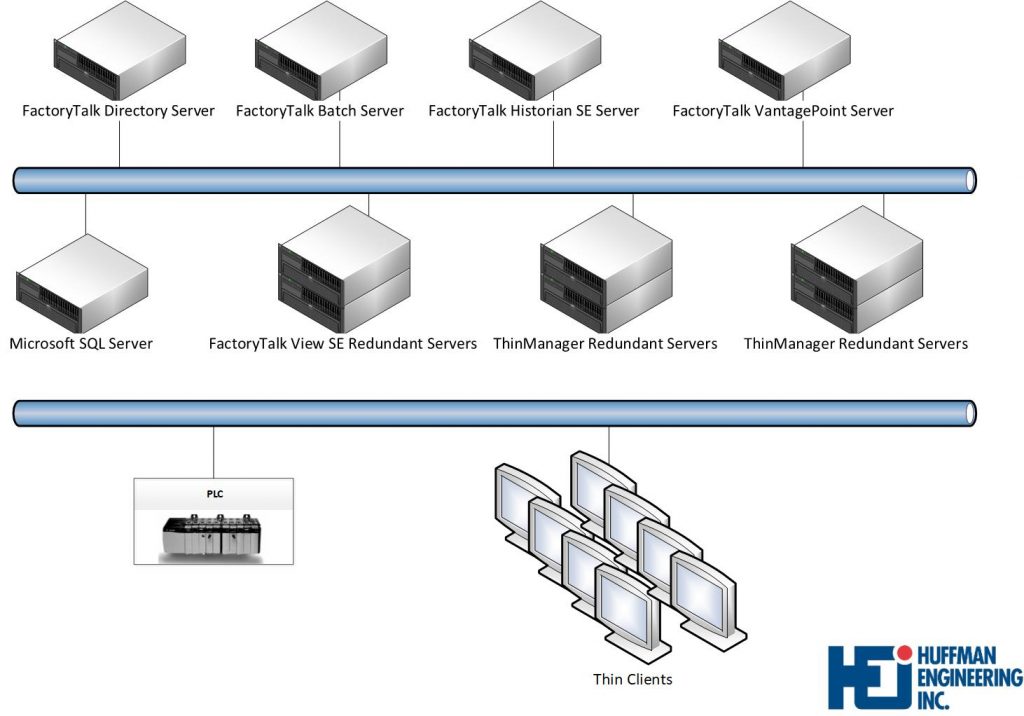
Huffman Engineering, Inc. is an engineering services firm specializing in control system integration and serving the Midwest. Our start-to-finish project expertise includes design, development, implementation, support, testing, and training.