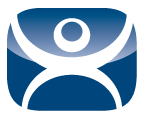
Every Friday, we dedicate this space to sharing solutions for some of the most frequently asked questions posed to our ThinManager Technical Support team. This weekly feature will help educate ThinManager Platform users and provide them with answers to questions they may have about licenses, installation, integration, deployment, upgrades, maintenance, and daily operation. Great technical support is an essential part of the ThinManager Platform, and we are constantly striving to make your environment as productive and efficient as possible.
We are currently running ThinManager on a Windows 2003 server. We have added McAfee antivirus software to the server and we are seeing a difference in the performance of the server and ThinManager. Do you have any suggestions as to certain exclusions that need to be added to the antivirus software to allow ThinManager to continue running with acceptable performance??
Add exceptions for ThinServer.exe, ThinServerProxy.exe, and ThinManager.exe to your exceptions. They are all located in: C:\Program Files\Automation Control Products\ThinManager.
-TM
_______________________________________
In the past we had some issues with the DOC. One of our ThinManager ready thin clients failed and it had to be changed. The current hardware and the DOC was not compatible with the new hardware. What is the procedure if this would happen in the future?
If the Thin Clients have the Disk on Chip Update Module installed, it should be removed before any upgrade. This will eliminate the possibility of the DOC being inadvertently updated. The DOC is tied to a specific model number, so if a thin client dies it will have to be replaced with the same model number. If replacements cannot be found/purchased, then we can create a new DOC for you.
-TM
_________________________________________
We have ThinManager v3.1 and would like to confirm if this is supported on Windows Server 2008. If not, then what version of ThinManager is required to be supported with 2008 and what versions of 2008 does that support?
Just a heads up, we no longer support TM 3.1, but we can definitely assist with transferring of licenses.
ThinManager 4.0+ is fully compatible with Windows 2008.
ThinManager 5.0 SP2+ is fully compatible with Windows 2008 R2.
-TM
_______________________________________________________
I configured a terminal to show a single application. When the thinclient starts it shows desktop even when the AppLink checkbox is checked. What Im missing?
It sounds like terminal services is set to not allow initial programs.
– Go to Start > Administrative Tools > Remote Desktop Services (Terminal Services) > Remote Desktop Host Configuration.
– Right click on RDP-Tcp and select properties.
– Go to the Enviroment tab and verify that it’s set to “Run initial program specified by user profile…”
-TM
______________________________________________
To review the cost savings of using the ThinManager Platform, visit our ROI Calculator here.
To read about successful ThinManager Platform deployments, visit here.
To see when the next ThinManager 2-Day Training Session is being offered, visit here.